TRUST IN ANSTEE COIL TECHNOLOGY
Every day, every month and every year since 1948, somewhere in the world, industry has trusted an Anstee Group company for reliability, performance, quality and innovation.
-
Wind Generators
Low Voltage coils for all applications.
-
Electromagnetic Flowmeter Coils
Freestanding self-bonded coils with nominal diameters (DN) ranging from 2 mm to 3,000 mm.
-
Coriolis Coils
High and low temperature and ATEX approvals.
-
Lighting
Chokes, Resistors and Ballast Coils for industrial and domestic lighting equipment.
-
Solenoid Coil and Latching Devices
From fine-gauge bobbin-wound coils to freestanding self-bonded heavy-duty coils.
-
Cables and Wiring
Ultra-high-temperature bespoke cable and loom harnesses.
-
Sensing Devices
Design assistance and manufacture of bespoke sensing devices tailored to your needs.
-
Did You Know?
Since we started making copper coils in 1948, our coil has been used in some interesting technology and places. Find out more...
WATCH OUR VIDEO
TAKE THE FACTORY TOUR
Look behind the scenes at one of our factories to see how our local teams make world-class, market-leading electromagnetic coils for global applications.

Our experienced senior management team brings over 100 years’ combined knowledge and experience in electromagnetic coil technology. From left to right: Barry Hood (director), Mark Trigg (CEO) and our chairman, Jonathan Anstee, whose grandfather founded the business in 1948.
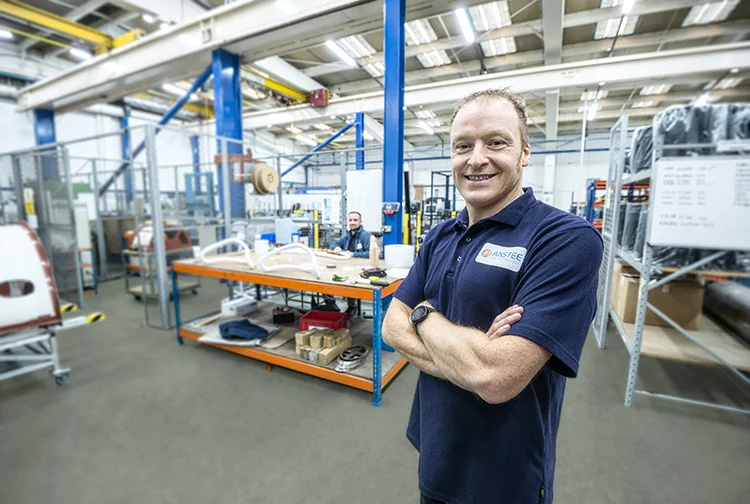
Experienced production managers set the example for taking pride in work with orderly factories that support a methodical approach to fulfilling your bespoke or off-the-shelf order.

Our stores management continues the tidy, organised theme with consignment stock for call off or shipping-to-factory under our vendor-managed inventory (VMI) and kanban systems.

From medical applications to massive water pipelines, our proprietary manufacturing equipment gives us unique capability to make your bespoke coils in diameters ranging from 0.2 mm to 3,000 mm.

In 2017, over 50% of the coils we make are bespoke – unique products designed, prototyped and skilfully manufactured to customers’ exact specifications before despatch around the world.

Highly-skilled technicians regularly work with specialised exotic materials. Here, one of the team concentrates on applying insulation to protect another bespoke flowmeter coil. The carefully wound insulation provides mechanical protection against temperatures up to 400 °C when the coil is positioned in its outer tube.

As well as bespoke coils, we hold generous stocks of carefully stored coils ready for 48-hour off-the-shelf delivery under vendor-managed inventory (VMI) and kanban.

After putting so much care and attention to detail into making your coil, it deserves maximum protection and careful handling from our factory stores to your goods-inwards point.

You want braised, rather than soldered connections for a high-performance joint in a high-temperature application? Tell us exactly what you need and we’ll assist with your design and manufacture a bespoke product. Maybe a coil like this one, to which a connecting cable is being attached.

At production facilities on three continents, we pair innovative proprietary machinery with highly-skilled manual craftsmanship to apply the finishing touches to your product – always to the same high standards.

Professional coil technicians (seen here brazing connecting wires to a copper coil) bring years of experience to your bespoke or off-the-shelf order. Low employee turnover reflects excellent team morale and keeps hard-won expertise and skills within a family-run company that now operates globally on several continents.

At any time, we hold around 5,000 Km of copper wire in rapidly accessible high-security storage. That’s enough wire to link London (UK) to Boston (USA) across the Atlantic Ocean. Keeping high stock levels, and carefully nurturing strategic partnerships with suppliers, is vital to quickly fulfil your order.

Every one of the c.174, 000 coils we make each year is physically checked. Here, one of the team demonstrates our obsessive attention to quality during a routine dimensional check. Attention to detail reduces waste and enables savings that we pass on to customers wherever possible.

From accurate winding and skilful, intricate connection methods to precision manufacture and installation of cable assemblies, attention to detail throughout coil manufacture is vital for reliable long-term performance.

Speed, dexterity, focus and absolute concentration by experienced technicians complements the specialised tooling that we provide for bespoke products. Here, one of our UK production team works fast, accurately and without compromising quality while removing coils from a winding machine.

Carefully planned and monitored stockholding complements highly-skilled specialist manufacturing. The result? On-time deliveries to customers around the world arrive when we say they will.

There are no compromises with our quality control checks. Here, dimensional checks are being done on another coil as it nears completion. During 2017, computerised measuring machines (CMMs) will complement our team’s human skills for the first time. This will further increase accuracy and conformity monitoring.

Our talented production operatives regularly hand-make over 600 fine-gauge bobbin coils in a day using hair-thin 0.05 mm copper wire and their precision-manufacturing skills. The largest coils we manufacture may be 300-times the size of these mini-masterpieces, but we always take the same care during their manufacture.

Stocks of off-the-shelf coils ready for despatch. Coolpolymer is a unique moulding product that conducts heat away from the coil for better performance and reliability in the most demanding high-temperature applications.

Any electromagnetic coil is only as good as the condition it is in when it reaches you. That’s why we continuously improve our bespoke packaging to protect your order, avoid transit damage and make sure even the smallest coil arrives in perfect condition – whether locally, regionally or on the other side of the world.

This tiny high-temperature bobbin coil will eventually be used in other products. Here, specially formulated varnish is precisely hand-applied to protect your coil against the effects of temperature and the atmosphere during its service life.

This winding machine shows another example of the special tooling and equipment that we make in-house and use at our factories on three continents. It’s vital for manufacturing bespoke electromagnetic coils that meet the most demanding customer requirements.

A highly-skilled workforce complements our proprietary special tooling and decades of expertise. Most team-members have been with us for many years. Such continuity of commitment and the resulting low staff turnover helps ensure the consistent high quality that customers expect from Anstee Coil Technology.

Careful handling is essential at every stage of coil manufacture. Here, a coil wound on a ceramic bobbin for high-temperature applications is removed from one of our winding machines.

Years spent working on different stages of coil manufacture mean team-members can move quickly between different tasks so that your order is fulfilled on time.

This DN 2,000 mm coil demonstrates the wide range of bespoke and off-the-shelf coil sizes that we make at our factories in the UK, China and (from late 2017) Mexico. Wherever you are in the world, if you need a bespoke coil with a diameter between 2 mm and 3,000 mm, we can manufacture it.

An electromagnetic coil before (left) and after (right) applying specialist insulation. Doing this for high-temperature applications may look simple, but demands intense concentration, attention to detail and experience to ensure your coil’s long-term performance and reliability.

We always keep large stocks of copper wire in our high-security warehouses. This means we can meet customer orders quickly, with many orders being fulfilled within just two days. With approximately 5,000 km of wire in stock at any time, there’s enough to stretch across the Atlantic Ocean from Boston, Massachusetts to London, England!

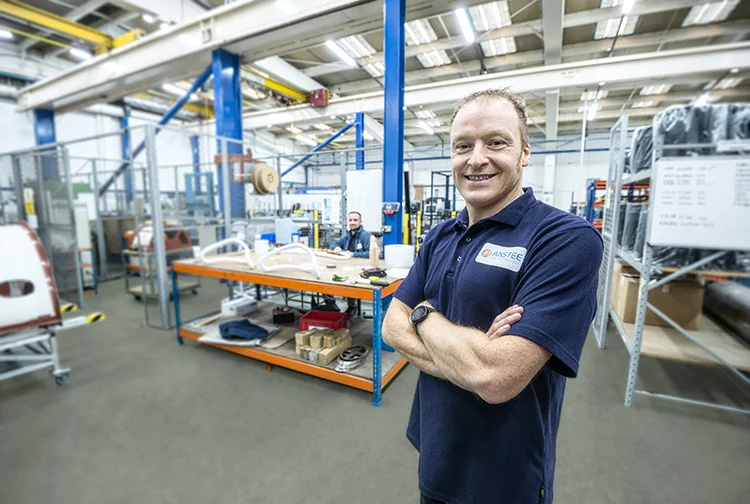

























